An Introduction to Optical Coatings
This is Sections 11.1, 11.2, and 11.7 of the Laser Optics Resource Guide.
Optical coatings are used to enhance the transmission, reflection, or polarization properties of an optical component. For example, about 4% of incident light will be reflected at each surface of an uncoated glass component. An anti-reflection coating could be applied to reduce the reflection at each surface to less than 0.1% and a highly reflective dielectric coating could also be applied to increase reflectivity to more than 99.99%. An optical coating is composed of a combination of thin layers of materials such as oxides, metals, or rare earth materials. The performance of an optical coating is dependent on the number of layers, their thickness, and the refractive index difference between them. This application note discusses optical coating theory, different types of common coatings, and coating manufacturing methods.
Thin film optical coatings are typically created by depositing dielectric and metallic materials, such as tantalum pentoxide (Ta2O5), aluminum oxide (Al2O3), or hafnium oxide (HfO2), in alternating thin layers. In order to maximize or minimize interference, they are typically λ/4 optical thickness (QWOT) or λ/2 optical thickness (HWOT) of the wavelength of the light used in the application. These thin film layers alternate between high index of refraction and low index of refraction, thereby inducing the interference effects needed (Figure 1).
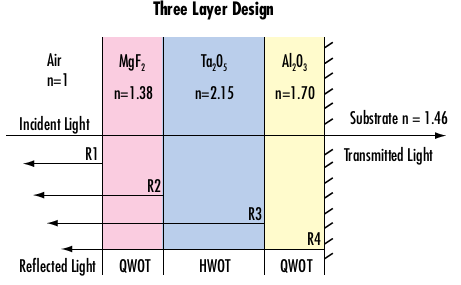
Figure 1: In a three-layer broadband anti-reflection (BBAR) coating, the correct choice of λ/4 and λ/2 thicknesses of coatings results in a high transmission and low reflection loss
Optical coatings are designed to enhance the performance of an optical component for a specific angle of incidence and polarization of light such as s-polarization, p-polarization, or random polarization. Using the coating at a different angle of incidence or polarization than what it is designed for will result in a significant degradation in performance. Sufficiently large deviations in incidence angle and polarization can result in a complete loss of coating function.
Optical Coating Theory
The Fresnel equations of refraction and reflection must be understood in order to comprehend optical coatings. Refraction is the change in direction of a wave’s propagation as it passes from one optical medium to another and is governed by Snell’s law of refraction:
n1 is the index of refraction of the incident medium, θ1 is the angle of the incident ray, n2 is the index of the refracted/reflected medium, and θ2 is the angle of the refracted/reflected ray (Figure 2).
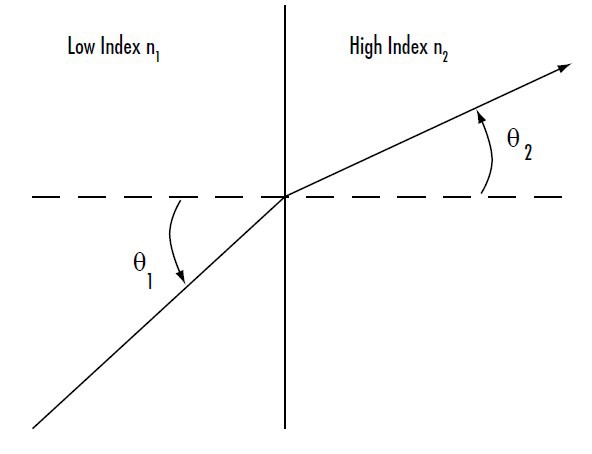
Figure 2: Light moving from a low index medium to a high index medium, resulting in the light refracting towards the interface normal
The angle of a ray anywhere in a multilayer thin film coating consisting of plane parallel surfaces of different refractive indices can be found using Snell’s law. The internal angle of the ray in the film is independent of the film order or the location of the film in the stack because Snell’s law applies at each interface (Figure 3):
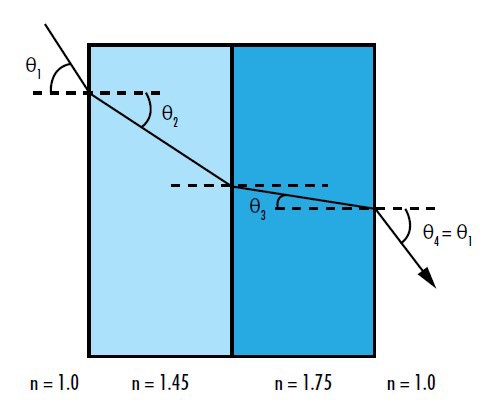
Figure 3: The refracted angle of a ray at any layer in a multilayer thin film coating consisting of plane parallel surfaces is independent of the layer order and can be found using Snell's law
The exiting ray in Figure 3 will be parallel to the incident ray because n1 = n4. Optical coatings on curved surfaces are not truly plane parallel structures due to the curvature of the optic. However, this approximation is still valid due to the thinness of the coatings.1
The law of reflection states that the angle of a reflected ray, with respect to the surface normal, is of equal magnitude to the angle of incidence, but of opposite direction with respect to the surface normal.
If the angle of incidence of a ray passing from one medium to another with a lower refractive index is larger than the critical angle of a material (θC) defined by the ratio of the two refractive indices, total internal reflection will occur and the ray will be completely reflected (Figure 4). The angle of refraction equals 90° when the incident angle is exactly equal to the critical angle.2
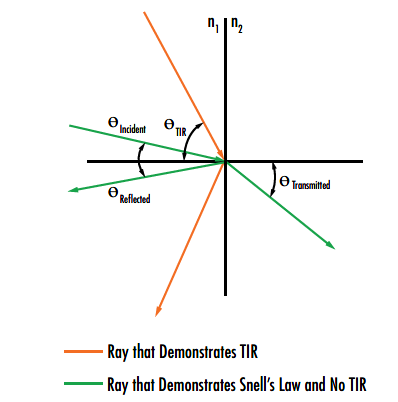
Figure 4: Demonstration of total internal reflection (TIR) where the incidence angle is larger than Θc
Where ts and tp are the amplitude transmission coefficients for s- and p-polarization, rs and rp are the amplitude reflection coefficients for s- and p-polarization, n1 and n2 are the refractive indices of the two optical media, θ1 is the incident angle, and θ2 is the transmitted or reflected angle. At normal incidence, θ1 and θ2 are 0 making all cosine terms 1 and the amplitude coefficients the same for both polarization states. This makes intuitive sense as there is no distinction between the s- and p-polarization states at normal incidence.
Please accept marketing-cookies to watch this video.
Reflection occurs when light strikes electrons on the surface of the material it is entering. The electrons absorb and re-emit the light with some energy loss. Shiny, highly reflective mirrored materials have more electrons with free mobility, leading to maximum reflection and minimal transmission.
Coating Technologies
There are several physical vapor deposition technologies commonly used to apply optical coatings including ion-assisted electron-beam evaporative deposition, ion beam sputtering, advanced plasma deposition, and plasma-assisted reactive magnetron sputtering (Table 1). No single coating technology is the ideal choice for every application, as each technology has unique strengths that make it optimal for some specific and overlapping use cases.
E-Beam IAD | APS | PARMS | IBS | |
Spectral Performance |
Stable | Stable | Stable | Very Stable |
Coating Stress | Low-Medium | Medium-High | Medium-High | High |
Repeatability | Med-High | High | High | Very High |
Layer Density | Med-High | High | High | Very High |
Layer Smoothness | Med-High | High | High | Very High |
Process Time | Fast | Intermediate | Slow-Intermediate | Slow |
UV Capability | High | Medium-High | Medium | Low-Medium |
Substrate Geometry | Very Versatile | Versatile | Limited | Limited |
Relative Price | $ | $$ | $$ | $$$ |
Table 1: The key parameters of common coating technologies show that the ideal coating technology for a given situation is highly application dependent (E-Beam IAD: ion-assisted electron-beam evaporative deposition, IBS: ion beam sputtering, APS: advanced plasma deposition, and PARMS: plasma assisted reactive magnetron sputtering)
Ion-Assisted Electron-Beam Evaporative Deposition
Ion-assisted electron-beam (IAD e-beam) evaporative deposition is a coating technique in which an electron gun bombards and vaporizes source materials in a vacuum chamber. The resulting vapor condenses onto optical surfaces and forms uniform, low-stress layers of specific designed thicknesses. IAD e-beam coatings feature low losses in the ultraviolet (UV) spectrum and high laser-induced damage thresholds (LIDTs) in the near infrared (NIR) spectrum. This technique also offers more flexibility for coating design than other methods, as it can use the widest range of useable materials. IAD e-beam evaporative deposition machines also produce coatings at a lower cost than other methods and accommodate larger coating chamber sizes. This coating technology is ideal for situations when flexibility and cost are the top priorities over high performance. Depending on the exact ion source used, this technique can result in coatings with lower densities, limited smoothness and reflectivity, and less repeatable properties. This can make precise layer thickness control more challenging than when using ion beam or magnetron sputtering. For this reason, IAD e-beam evaporative deposition cannot create extremely low or high reflectivity coatings, such as an antireflection V-coat with 99.95% transmission at 1064nm.
Ion Beam Sputtering
Ion beam sputtering (IBS) is a highly-repeatable coating technology that creates coatings of very high optical quality and stability. During IBS, a high-energy beam of ions bombards a target of the desired coating material, causing target atoms to “sputter” off the target (Figure 5). The target atoms experience a significant kinetic energy (~10’s to 100’s eV), which causes them to form a dense, hard, and smooth film on the surface of optical components.5 One of the main advantages of IBS is that it allows for precise monitoring and control of parameters including layer growth rate, oxidation level, and energy input, resulting in highly repeatable coatings. High-speed substrate rotation also contributes to exceptional layer thickness accuracy. This allows IBS to create some of the most demanding optical coatings, including ultra-low loss mirrors with reflectivity values above 99.9%, chirped mirrors for ultrafast laser applications, and filters with very sharp spectral transitions. The performance of IBS coatings is also less affected by environmental factors, such as temperature and humidity, than that of other coating technologies. However, there are several drawbacks to IBS coatings, including higher stress and loss in the UV spectrum. Slower growth rates and chamber sizes also lead to a significantly higher relative cost than other coating methods, which limits IBS to certain applications when high performance is required.
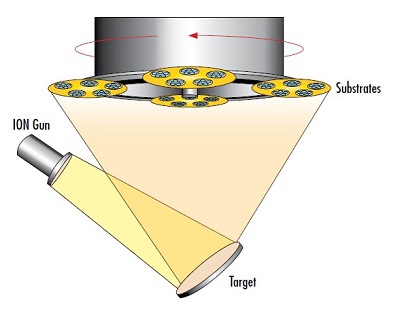
Figure 5: IBS is a highly-controllable process which utilizes a high-energy ion gun to sputter material off a target onto rotating substrates, resulting in very accurate and repeatable optical coatings
Advanced Plasma Sputtering
Advanced plasma sputtering (APS) is a modified version of IAD e-beam evaporative deposition that benefits from advanced automated processing capabilities. APS utilizes a hot cathode DC glow discharge plasma instead of an ion beam to deposit coating material. The plasma fills the entire coating chamber, releasing target ions and depositing them on optical surfaces. APS results in smooth, dense, and hard coatings that offer more stable optical properties than IAD e-beam while keeping IAD e-beam’s high level of versatility. APS can also deposit coatings in volume at a similar price structure to IAD e-beam evaporative deposition, making it preferable when large volumes of coatings with slightly more demanding performance requirements. However, APS experiences higher stress, has more loss in the UV spectrum, and requires iterative process development which leads to a slightly higher cost compared to IAD e-beam evaporative deposition. In many aspects, APS, along with magnetron sputtering, can be considered an intermediate solution for many parameters between IAD e-beam evaporative deposition and IBS.
Plasma Assisted Reactive Magnetron Sputtering
Plasma assisted reactive magnetron sputtering (PARMS) is another plasma generation-based coating technology. A glow discharge plasma is generated like in APS, but a magnetic field “confines” it near the target instead of filling the entire coating chamber. The plasma accelerates positive ions onto the target, ejecting target atoms which deposit onto optical surfaces. PARMS operates at a relatively low chamber pressure at high efficiency because of the confinement of the plasma. This low pressure reduces setup time and allows for more economical coating of high-volume optics. Thin-film coatings formed by PARMS are hard and dense due to reactive gasses added to improve the stoichiometry of the coatings. PARMS is highly repeatable, but not as highly a repeatability as IBS. However, PARMS has a higher throughput, making it an appealing middle ground between the high price and performance of IBS with more economical coating technologies such as IAD e-beam evaporative deposition. PARMS is often used to manufacture fluorescence filters because of the technology’s balance of relatively high optical performance and relatively high-volume throughput.
References
- Willey, Ronald R. Field Guide to Optical Thin Films. SPIE Optical Engineering Press, 2006.
- Greivenkamp, John E. Field Guide to Geometrical Optics. SPIE Optical Engineering Press, 2004.
- Paschotta, Rüdiger. Encyclopedia of Laser Physics and Technology, RP Photonics, October 2017, www.rp-photonics.com/encyclopedia.html.
- Vandendriessche, Stefaan. “No One-Size-Fits-All Approach to Optical Coatings.” Photonics Spectra, Photonics Media, December 2016.
- “IBS Mirror Coatings for Highly Demanding Applications.” Photonics News, Laser Components Group, August 2016, www.lasercomponents.com/uk/news/ibs-mirror-coatings-for-highly-demanding-applications
More Resources
- Anti-Reflection (AR) Coatings Application Note
- Metallic Mirror Coatings Application Note
- Highly Reflective Coatings Application Note
- Laser Optics Lab: Coatings Video
- Understanding and Specifying LIDT of Laser Components Application Note
- Modifying Stock Optics Tip #4: Add A Coating To A Stock Lens Video
- Benefits of Hard Coatings Application Note
- High Reflectivity Mirrors for Laser Applications Webinar
- Laser Optics Lab Video Series
or view regional numbers
QUOTE TOOL
enter stock numbers to begin
Copyright 2023, Edmund Optics Inc., 101 East Gloucester Pike, Barrington, NJ 08007-1380 USA
California Consumer Privacy Acts (CCPA): Do Not Sell or Share My Personal Information
California Transparency in Supply Chains Act